Tesla Parts Manufacturing: Global Production Network Explained
Tesla’s global manufacturing network
Tesla has established a sophisticated global manufacturing network that span multiple continents. Unlike traditional automakers who much outsource most components, tesla maintain a higher degree of vertical integration, produce many critical parts in house while strategically source others from global suppliers.
Tesla’s major manufacturing facilities
Tesla operates several major manufacturing facilities around the world where various components and vehicles are produce:
Fremont factory, California
The Fremont factory serve as tesla’s first major vehicle assembly plant. This facility produce:
- Model s
- Model x
- Model 3
- Model y
Beyond vehicle assembly, the Fremont facility manufacture some vehicle components, include:
- Electric motors
- Battery packs (assembly )
- Certain interior components
Gigafactory Nevada
Locate in sparks, Nevada, this facility focuses mainly on battery production in partnership witPanasonicic. Key components produce here include:
- Battery cells (pPanasonicsection )
- Battery packs
- Drive units
- Energy storage products
The Nevada gigafactory represent tesla’s effort to bring battery production close-fitting to vehicle assembly to reduce costs and supply chain complexity.
Gigafactory New York
Locate in buffalo, this facility focus on:
- Solar panels
- Solar roof tiles
- Supercharger components
- Certain electrical components
Gigafactory shanghai
Tesla’s first manufacture facility outside the United States produce:
- Model 3
- Model y
- Battery packs
- Electric motors
- Various vehicle components for the Asian market
The Shanghai facility has become progressively important for tesla’s global production capacity, serve both the Chinese market and export to other regions.
Gigafactory Berlin Brandenburg
Tesla’s European manufacturing center produce:
- Model y (primary focus )
- Battery cells (plan )
- Battery packs
- Electric motors
- Plastic components
- Seats
Gigafactory Texas
Locate near Austin, this facility produce:
- Model y
- Cybertruck
- Battery cells (plan )
- Battery packs
- Electric motors
The Texas facility to serve as tesla’s current headquarters.

Source: guideautoweb.com
Key components and their origins
Battery cells and packs
Tesla’s battery supply chain is complex and evolving:
- In house production: Tesla produces some battery cells at gigafactoryNevadaa( in partnership with Panasonic) and is eexpandedin house production at other gigafactories
- Panasonic: Major supplier of battery cells at gigafactory Nevada and from facilities in Japan
- Lg energy solution: Supplies cells for certain tesla models, specially in China
- CATL: Chinese battery manufacturer supply cells for tesla vehicles produce in China
Battery pack assembly occur chiefly at tesla’s gigafactories, bring unitedly cells with thermal management systems, battery management electronics, and structural components.
Electric motors
Tesla design its electric motors in house and manufacture them at several locations:
- Gigafactory Nevada (drive units )
- Fremont factory (certain motor components )
- Gigafactory shanghai (motors for aAsianmarket vehicles )
- Gigafactory Berlin (motors for eEuropeanmarket vehicles )
- Gigafactory Texas (motors for vehicles produce thither )
Tesla’s motor design has evolved importantly, from the original ac induction motors to newer permanent magnet motors in more recent models.
Electronics and computer hardware
Tesla’s advanced electronics come from various sources:
- In house design: Tesla designs many electronic components and systems in house
- Autopilot hardware: Custom chips design by tesla, manufacture by Samsung in Texas
- Infotainment systems: Components source from various suppliers, assemble by tesla
- Battery management systems: Design by tesla, with components from various electronics suppliers
Body components and chassis
The vehicle structure come from multiple sources:
- Stamped body panels: Produce at tesla’s manufacture facilities
- Aluminum components: Source from global suppliers, with some produce in house
- Cast components: Progressively produce use tesla’s giant cast machines at their gigafactories
- Steel: Source from various steel manufacturers globally
Tesla has pioneered the use of large single piece castings to replace dozens of individually stamp and joined parts, simplify production.
Interior components
The interior parts come from a mix of in house production and suppliers:

Source: bloomberg.com
- Seats: Manufactured in house at some facilities, with components source from suppliers
- Dashboard components: Mix of in house production and supplier source parts
- Upholstery materials: Source from specialized suppliers
- Glass and displays: Source from specialized manufacturers
Suspension and drivetrain components
These critical mechanical parts come from:
- Suspension components: Mix of in house production and specialized suppliers
- Brake systems: Principally source from automotive suppliers, with regenerative braking systems integrate with tesla’s drive units
- Wheels and tires: Wheels design by tesla, manufacture by specialized suppliers; tires source from major tire manufacturers
Tesla’s approach to parts manufacturing
Vertical integration strategy
Tesla employs a higher degree of vertical integration than most automakers. This approach allow tesla to:
- Maintain greater control over component design and quality
- Reduce dependence on external suppliers
- Drive innovation in critical components
- Potentially reduce costs in the long term
This strategy is especially evident in tesla’s approach to batteries, motors, and software areas where tesla maintains significant in house capabilities.
Regional manufacturing approach
Tesla has progressively adopted a regional manufacturing strategy, where:
- Vehicles and major components are produce close-fitting to end markets
- Each major region (nNorth America eEurope aAsia)have production capacity
- Supply chains become more localized to reduce shipping costs and delays
This approach help tesla reduce logistics costs and exposure to supply chain disruptions while meet local content requirements in various markets.
Evolution of manufacturing techniques
Tesla endlessly evolves its manufacturing processes:
- Miscasting: Use massive die-cast machines to create large single piece components
- Battery cell innovation: Develop new cell formats and chemistry
- Automation: Implement advanced robotics throughout production
- Software integration: Use software to improve manufacture precision and quality
Source of raw materials
Tesla’s components require various raw materials source globally:
Battery materials
- Lithium: Source from Australia, Chile, china, and progressively from North American sources
- Nickel: Source from various global suppliers, with increase focus on responsible source
- Cobalt: Source from various locations, with tesla work to reduce cobalt content in batteries
- Graphite: Source principally from China and other Asian sources
Structural materials
- Aluminum: Source from global suppliers for body and structural components
- Steel: Source from various steel manufacturers, with increase use of advanced high strength steels
- Rare earth metals: Use in motors and electronics, source chiefly from China and other countries
Supply chain challenges and solutions
Recent supply chain disruptions
Tesla, like other automakers, has face supply chain challenges:
- Semiconductor shortages affect electronics production
- Raw material price volatility, specially for battery materials
- Logistics disruptions affect global shipping
- Regional manufacturing restrictions during global health crises
Tesla’s mitigation strategies
To address these challenges, tesla has implemented several strategies:
- Increase vertical integration: Bring more production in house
- Supply chain diversification: Reduce dependence on single sources
- Long term supplier agreements: Secure critical materials through contracts
- Regional production: Localize supply chains to reduce global shipping dependencies
- Component redesign: Adapt designs to use more available components
Aftermarket and replacement parts
Tesla’s approach to service parts
Tesla handle replacement parts otherwise from traditional automakers:
- Most replacement parts are available simply through tesla service centers
- Some components are remanufacture by tesla for service use
- Battery and drive unit replacements are typically refurbish units
- Body repair parts are available through certify collision repair centers
Third party parts ecosystem
A growth ecosystem of third party parts exist:
- Aftermarket accessories from various manufacturers
- Performance upgrades from specialized companies
- Alternative replacement parts for out of warranty vehicles
- Recycled parts from salvaged tesla vehicles
Future trends in tesla parts manufacturing
Increase localization
Tesla continues to move toward more localize production:
- Expand manufacturing in major markets
- Develop local supplier networks
- Reduce reliance on long distance shipping
Battery innovation
Battery technology remain a key focus:
- Expand in house cell production
- Develop new cell formats and chemistry
- Reduce dependence on rare or costly materials
- Increase battery lifespan and performance
Manufacturing process innovation
Tesla continues to innovate in manufacturing:
- Expand use of large castings to simplify production
- Implement advanced automation
- Develop new manufacturing techniques
- Increase production efficiency
Conclusion
Tesla’s parts manufacturing network span the globe, combine in house production with strategic supplier relationships. The company’s approach to vertical integration, regional manufacturing, and continuous innovation has created a unique supply chain that differ importantly from traditional automotive manufacturers.
As tesla continue to grow, its manufacturing footprint expands consequently, with increase localization of production in major markets. The company’s focus on key technologies like batteries, motors, and software guide its decisions about which components to produce in house and which to source from suppliers.
This complex global network enables tesla to produce its distinctive electric vehicles while maintain control over critical technologies and adapt to evolve market conditions and supply chain challenges.
MORE FROM feelmydeal.com
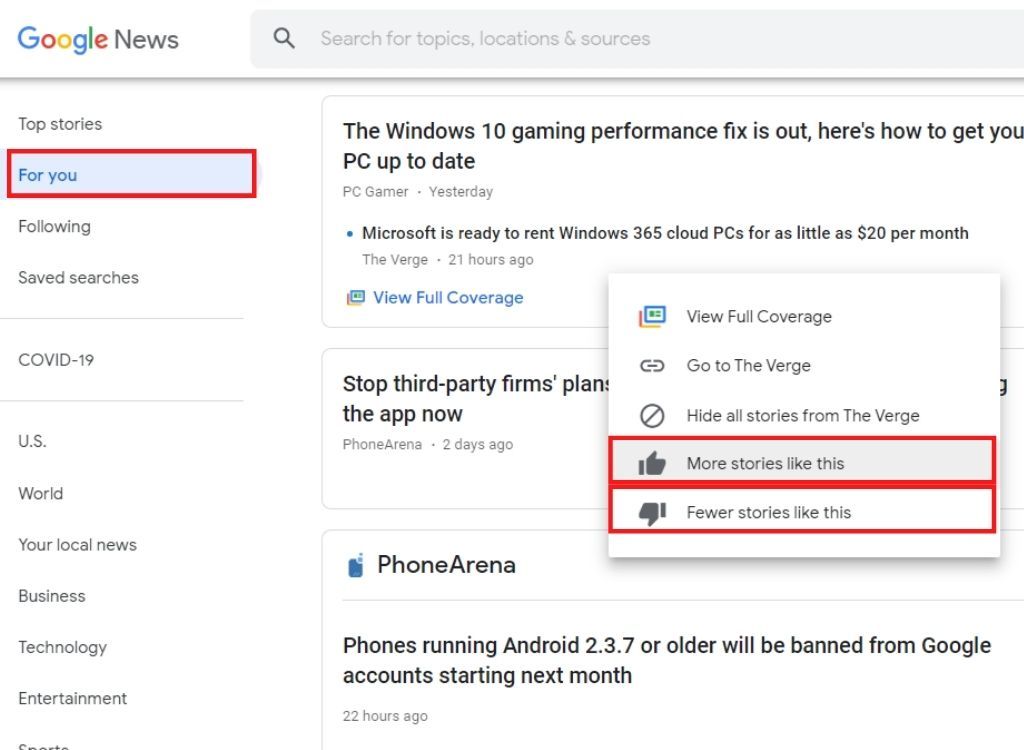
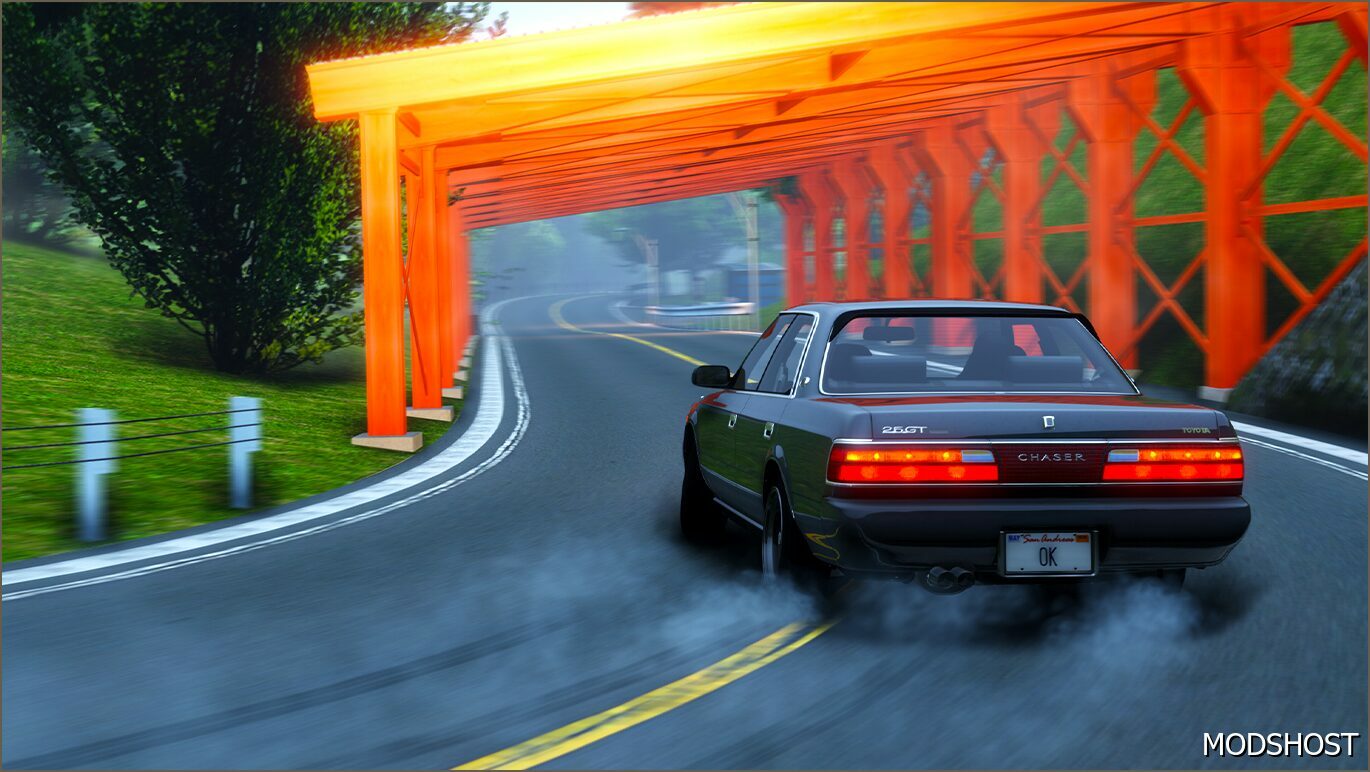
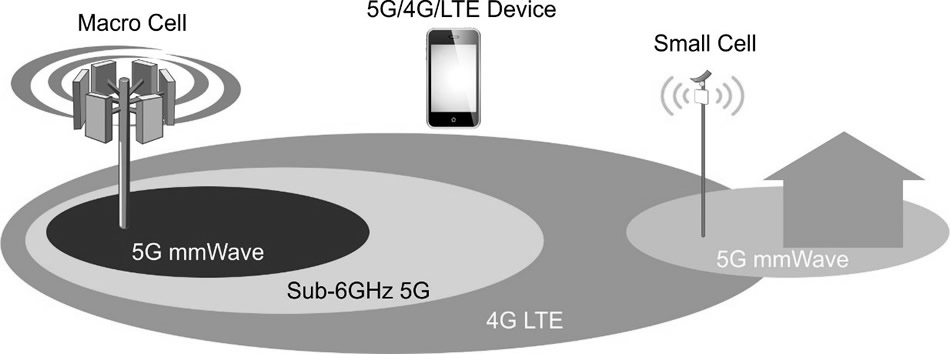
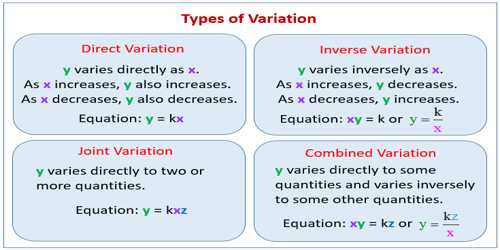
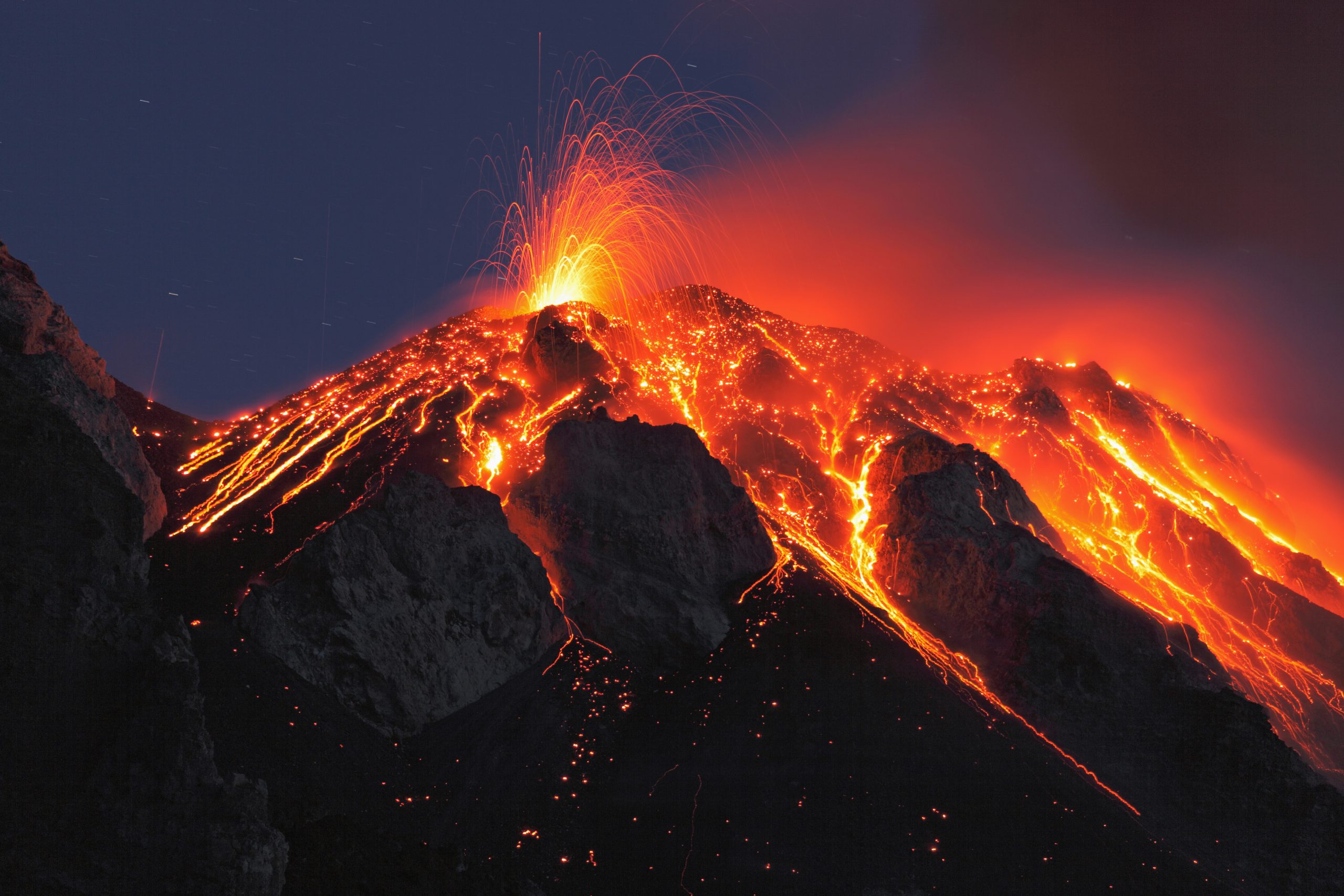
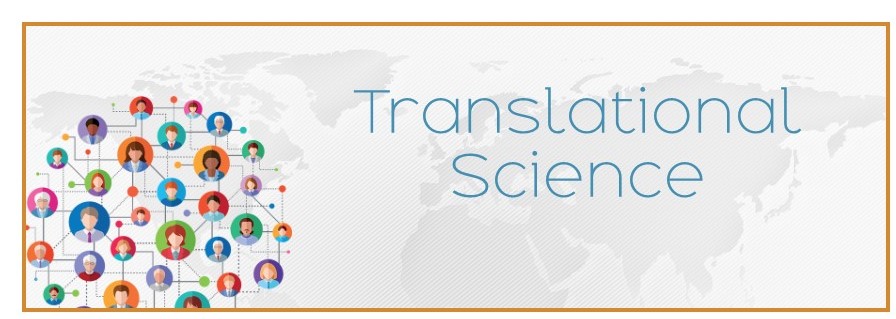
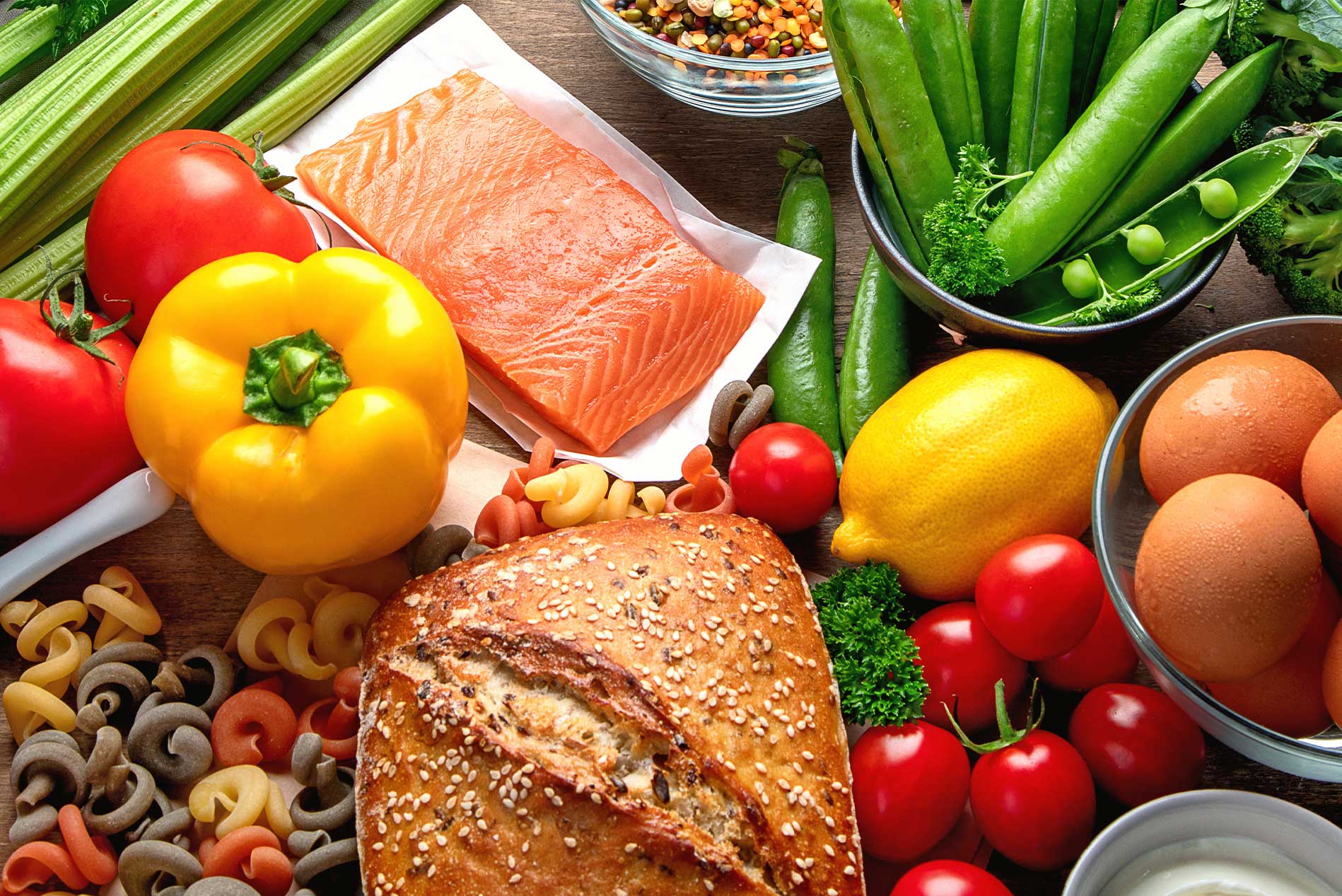
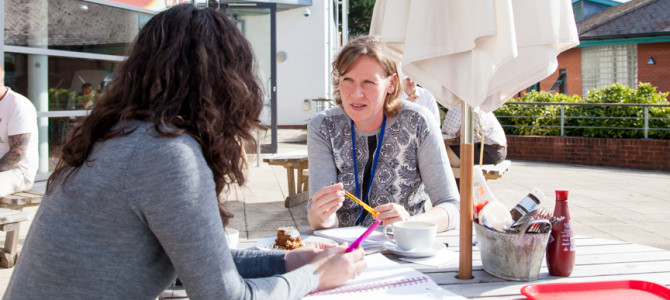
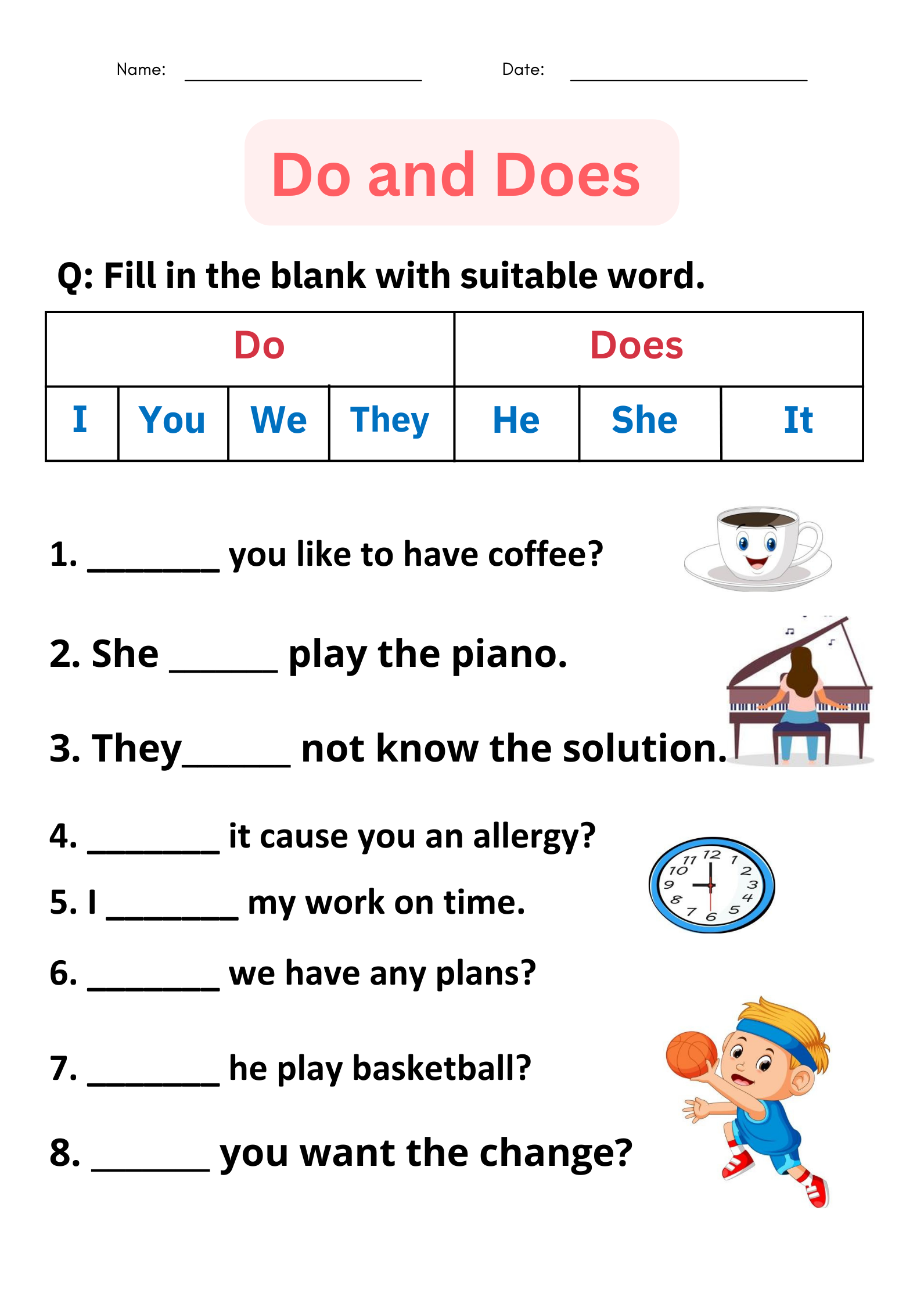
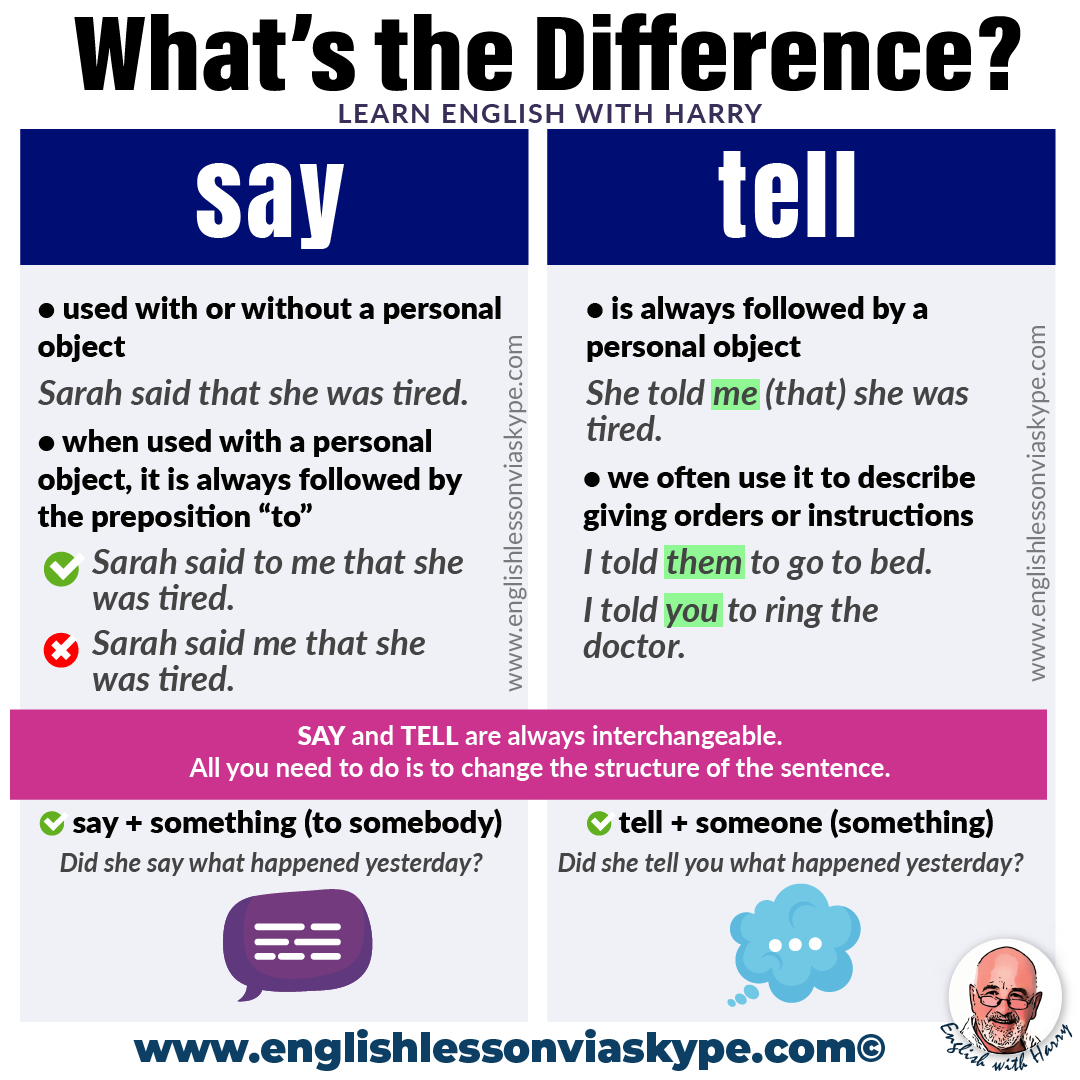
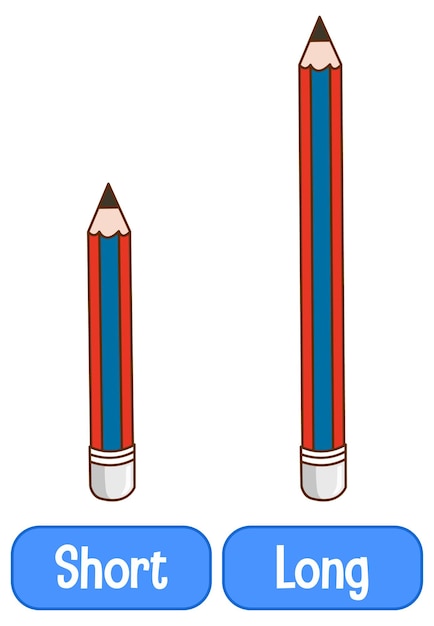
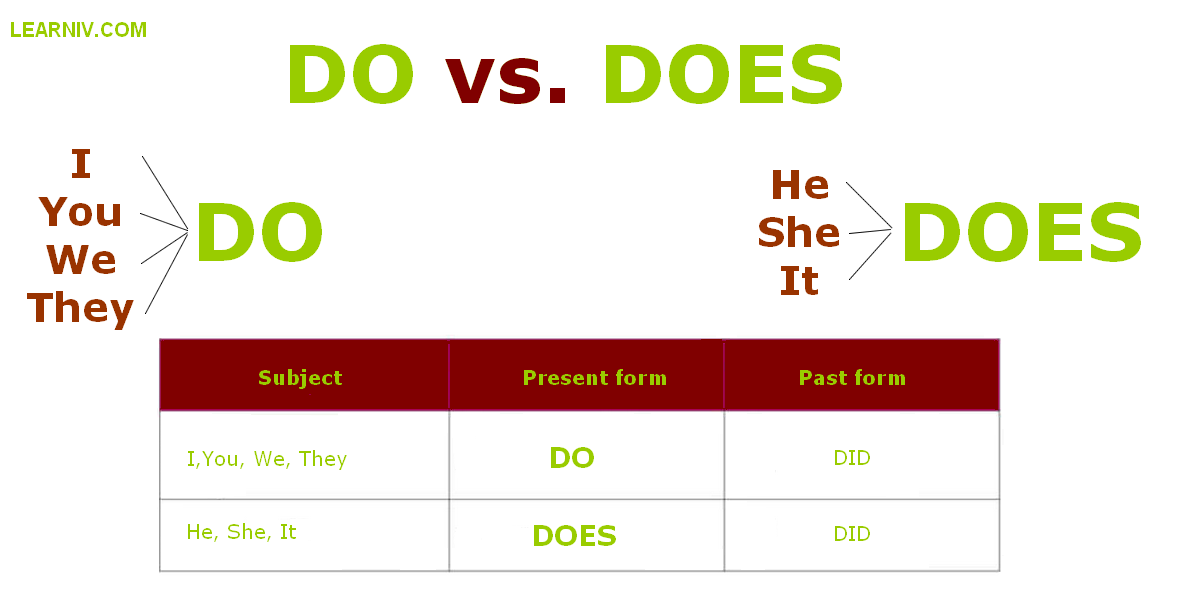