CAM Technology Applications: Industries and Companies Leading Manufacturing Innovation
Understand cam technology in modern manufacturing
Computer aided manufacturing (cam) technology represent a revolutionary approach to production processes, enable companies to automate and optimize their manufacture operations through sophisticated software systems. This technology bridge the gap between digital design and physical production, allow manufacturers to create precise, consistent products while reduce costs and improve efficiency.
Cam systems work by translate computer aid design (cad )files into mamachine-readablenstructions that control manufacturing equipment. These instructions guide everything from simple drilling operations to complex multi axis machining processes, ensure that each component meet exact specifications.
Aerospace and defense companies
Aerospace manufacturers stand among the virtually likely candidates for cam technology adoption. Companies like Boeing, Lockheed Martin, and airbus rely intemperately on cam systems to produce aircraft components that demand exceptional precision and reliability. The aerospace industry’s stringent quality requirements make cam technology essential for maintaining consistent production standards.
These companies manufacture components with complex geometries, tight tolerances, and exotic materials that require specialized machining techniques. Cam software enable them to program sophisticated five axis machining centers that can create intricate turbine blades, structural components, and engine parts that would be impossible to produce manually.
Defense contractors besides utilize cam technology extensively for produce military equipment, weapons systems, and specialized components. The need for precision, repeatability, and quality control in defense applications make cam systems indispensable for these organizations.

Source: markwideresearch.com
Automotive industry leaders
The automotive sector represents another major user of cam technology. Companies such asGeneral Motorss, ford,Toyotaa, andVolkswagenn integrate cam systems throughout their manufacturing processes to produce everything from engine blocks to body panels.
Automotive manufacturers benefit from cam technology’s ability to handle high volume production while maintain quality standards. The technology enable them to rapidly adapt to design changes, optimize tool paths for efficiency, and reduce waste in their manufacturing processes.
Tier one automotive suppliers besides intemperately invest in cam technology to meet the demanding requirements of original equipment manufacturers. These companies must produce components that fit utterly with other parts while meet strict quality and delivery schedules.
Medical device manufacturing
Medical device companies represent some of the virtually sophisticated users of cam technology. Organizations like Medtronic, Johnson & Johnson, and striker require cam systems to manufacture life critical devices that must meet FDA regulations and international quality standards.
The medical industry’s need for custom implants, surgical instruments, and diagnostic equipment drive cam technology adoption. These companies oftentimes work with biocompatible materials like titanium and specialized polymers that require precise machining parameters to maintain their properties.
Cam technology enable medical device manufacturers to produce small batches of extremely customize products, from patient specific implants to specialize surgical tools. The ability to promptly program and execute complex machining operations make cam systems essential for this industry.
Electronics and semiconductor companies
Electronics manufacturers, include companies like apple, Samsung, and intel utilize cam technology for produce precise components and assemblies. The miniaturization trend in electronics demands manufacturing capabilities that can achieve microscopic tolerances and work with delicate materials.
Semiconductor fabrication facilities rely on specialized cam systems to control the complex processes involve in chip manufacturing. These systems coordinate multiple manufacturing steps, from wafer preparation to final packaging, ensure consistent quality across millions of units.
Consumer electronics manufacturers use cam technology to produce housings, connectors, and mechanical components that must fit unitedly dead while maintain aesthetic appeal. The rapid product development cycles in electronics make cam systems valuable for promptly transition from design to production.
Tool and die manufacturing
Tool and die shops represent perchance the virtually intensive users of cam technology. These companies specialize in create the molds, die, and fixture that other manufacturers use in their production processes. Companies like macron, dmDMGomoreand countless smaller shops depend exclusively on cam systems for their operations.
The complexity of modern tooling require sophisticated cam programming to achieve the surface finishes and dimensional accuracy demand by customers. These companies oftentimes work with harden steels and exotic alloys that challenge both their equipment and programming expertise.
Tool and die manufacturers must invariably adapt to new materials, geometries, and customer requirements. Cam technology provide the flexibility need to tackle diverse projects while maintain profitability in a competitive market.
Energy sector applications
Energy companies, specially those in oil and gas, renewable energy, and nuclear power, utilize cam technology for manufacture critical components. Companies like General Electric, siemens, and Halliburton rely on cam systems to produce turbine components, drilling equipment, and power generation machinery.
The energy sector’s components oftentimes operate under extreme conditions, require precise manufacturing to ensure reliability and safety. Cam technology enable these companies to maintain the tight tolerances and surface finish necessary for optimal performance.
Wind turbine manufacturers use cam systems to produce large scale components like hub assemblies and gearbox housings. The size and complexity of these parts require sophisticated programming and machine coordination that cam technology provide.
Factors determine cam technology adoption
Several key factors determine which companies are virtually likely to implement cam technology. Production volume play a crucial role, as companies produce large quantities of parts benefit from the efficiency gains that cam systems provide.
Complexity requirements besides drive cam adoption. Companies manufacture parts with intricate geometries, multiple features, or tight tolerances find cam technology essential for maintain quality and consistency.
Material considerations importantly influence cam usage. Companies work with difficult to machine materials like titanium, income, or harden steels require the precise control that cam systems offer.
Quality standards represent another critical factor. Industries with strict regulatory requirements or zero defect mandates rely on cam technology to ensure consistent results and maintain traceability.
Implementation considerations
Companies consider cam technology must evaluate their current manufacturing processes, skill requirements, and return on investment. Successful implementation require train personnel who understand both the software and manufacturing processes.

Source: stripchat.com
Integration with exist systems present both opportunities and challenges. Companies must ensure their cam software work seamlessly with their cad systems, enterprise resource planning software, and machine tools.
The initial investment in cam technology can be substantial, include software licenses, training costs, and potential equipment upgrades. Yet, companies typically see returns through reduce setup times, improve quality, and increase production capacity.
Ongoing support and software updates represent additional considerations. Companies must budget for maintenance, training, and system upgrades to maximize their cam technology investment.
Future trends in cam technology
The evolution of cam technology continue to expand its applicability across industries. Artificial intelligence and machine learn integration promise to make cam systems more intelligent and adaptive.
Cloud base cam solutions are emerged, allow smaller companies to access sophisticated manufacturing capabilities without major infrastructure investments. This trenddemocratizese advanced manufacturing technology.
Additive manufacturing integration represent another significant development. Cam systems progressively support hybrid manufacturing processes that combine traditional machining with 3d printing technologies.
Industry 4.0 initiatives drive demand for cam systems that can communicate with other manufacturing systems, provide real time data and enable predictive maintenance capabilities.
Conclusion
Companies virtually likely to use cam technology share common characteristics: they manufacture complex parts, require high precision, work with challenging materials, or operate in regulated industries. Aerospace, automotive, medical device, electronics, and energy companies represent the primary users of this technology.
The decision to implement cam technology finally depend on a company’s specific manufacturing requirements, quality standards, and competitive pressures. As manufacturing become progressively complex, and customer demands will continue to will evolve, cam technology adoption will potential will expand across additional industries and company types.
Understand these applications and trends help manufacturers make informed decisions about cam technology investments and position them for success in a progressively competitive global marketplace.
MORE FROM feelmydeal.com
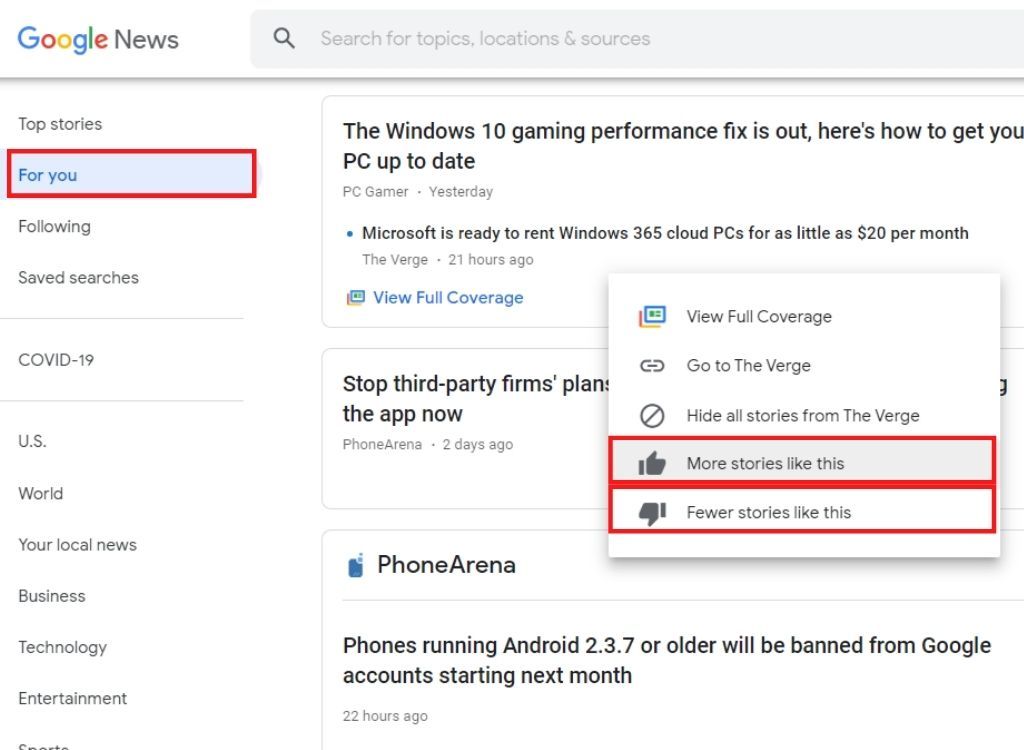
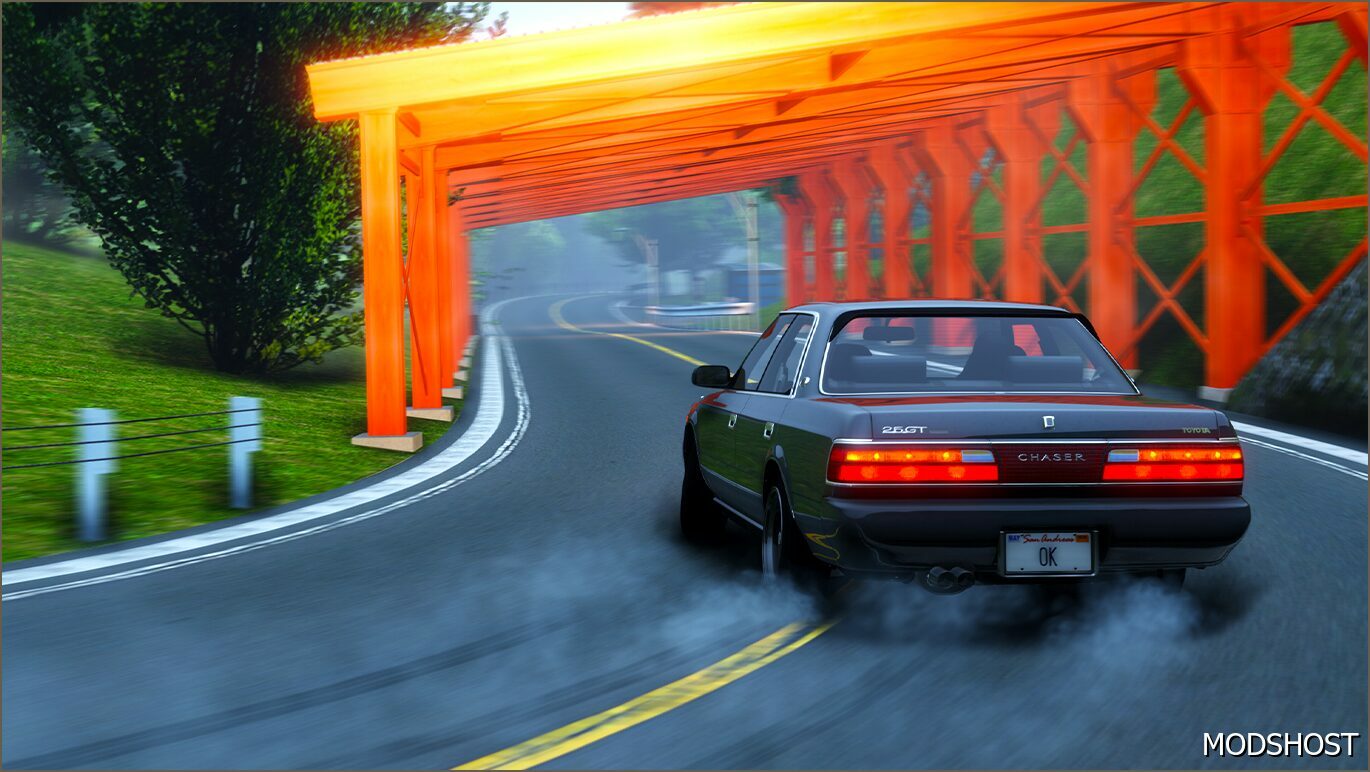
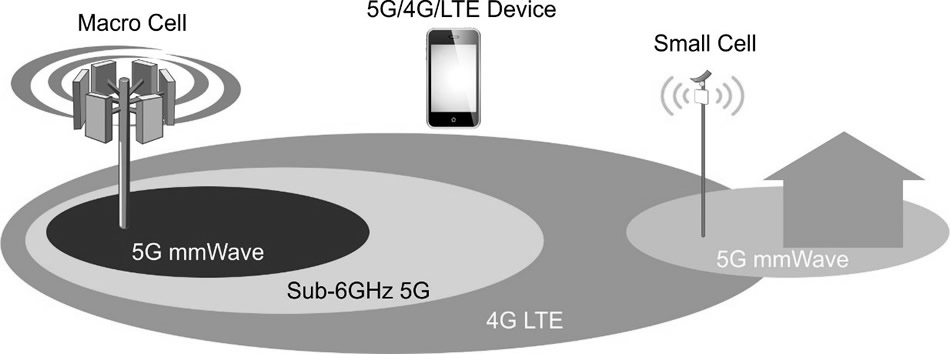
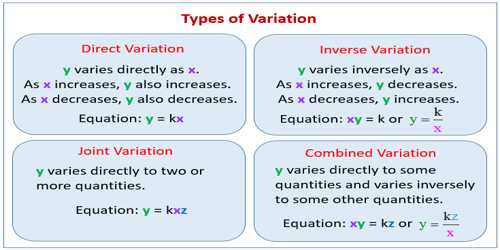
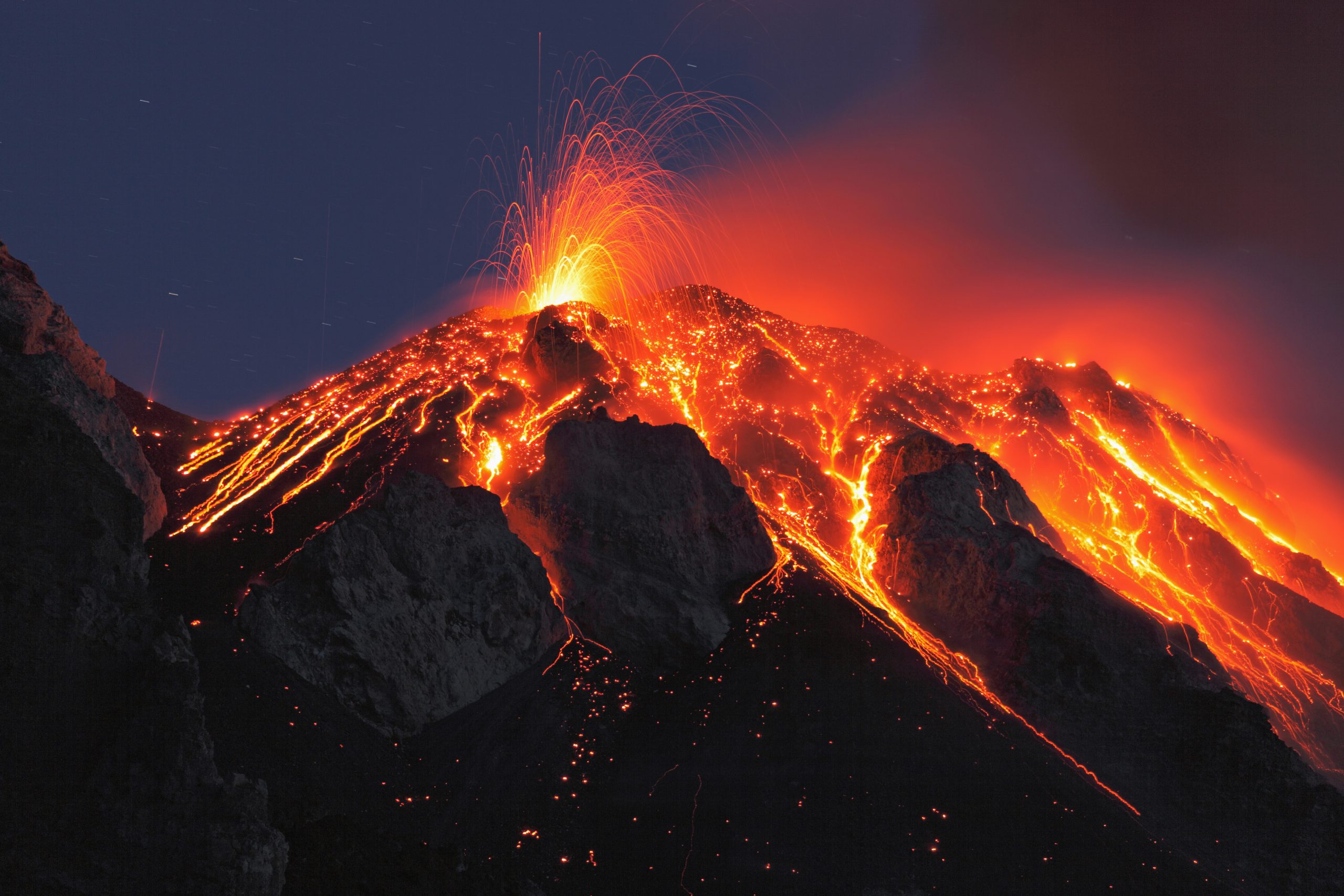
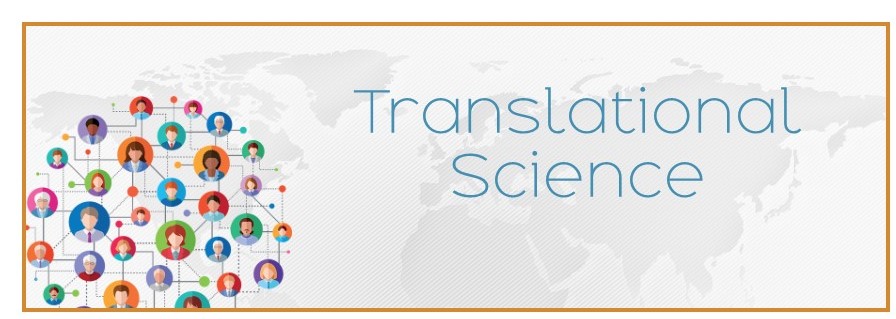
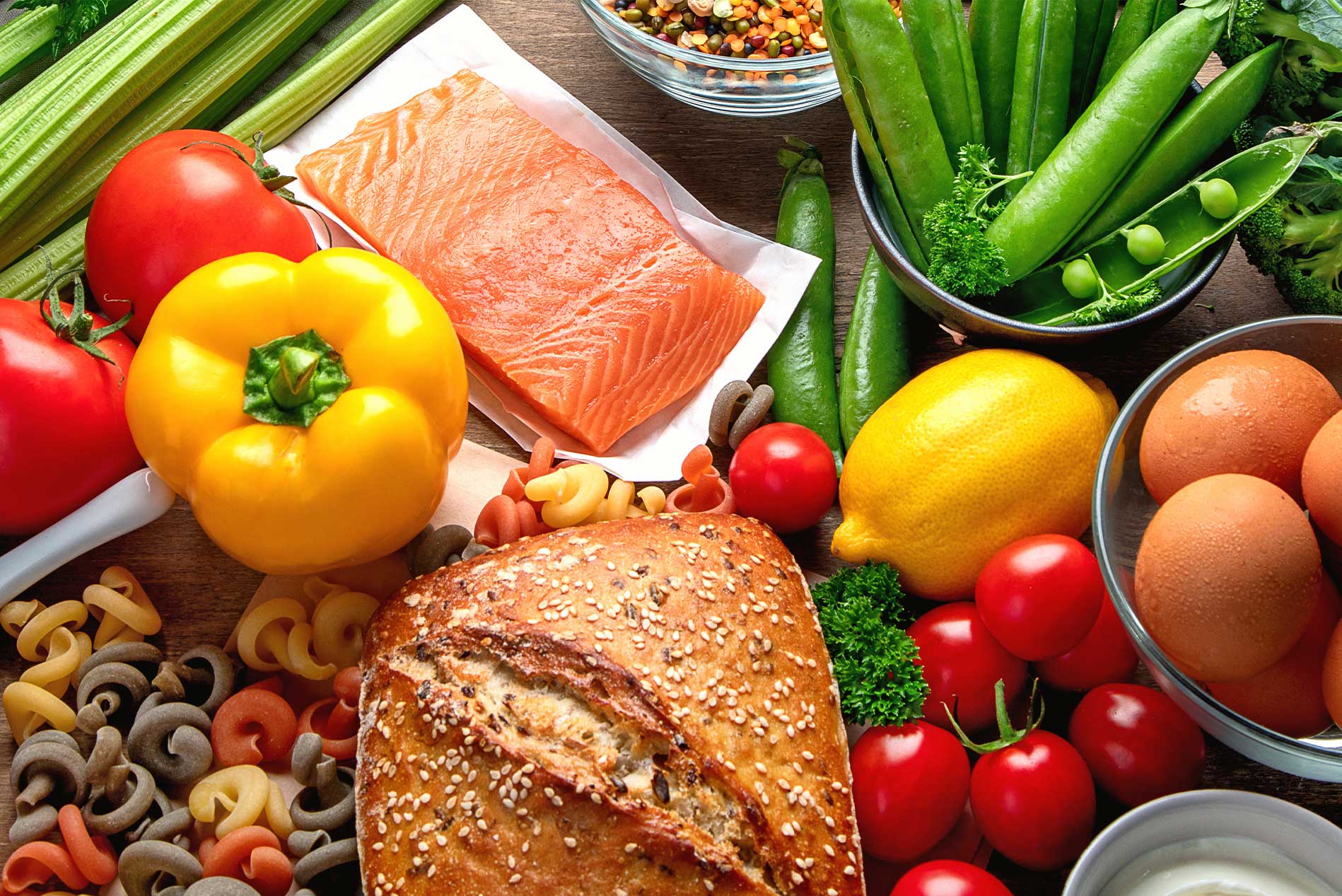
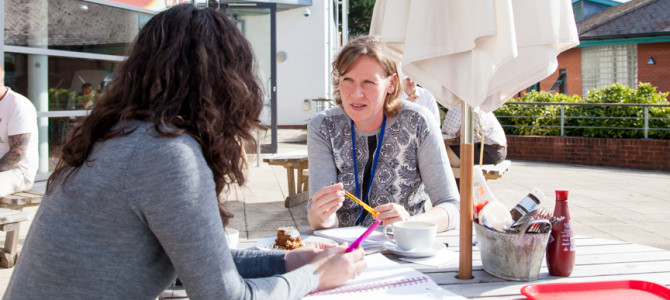
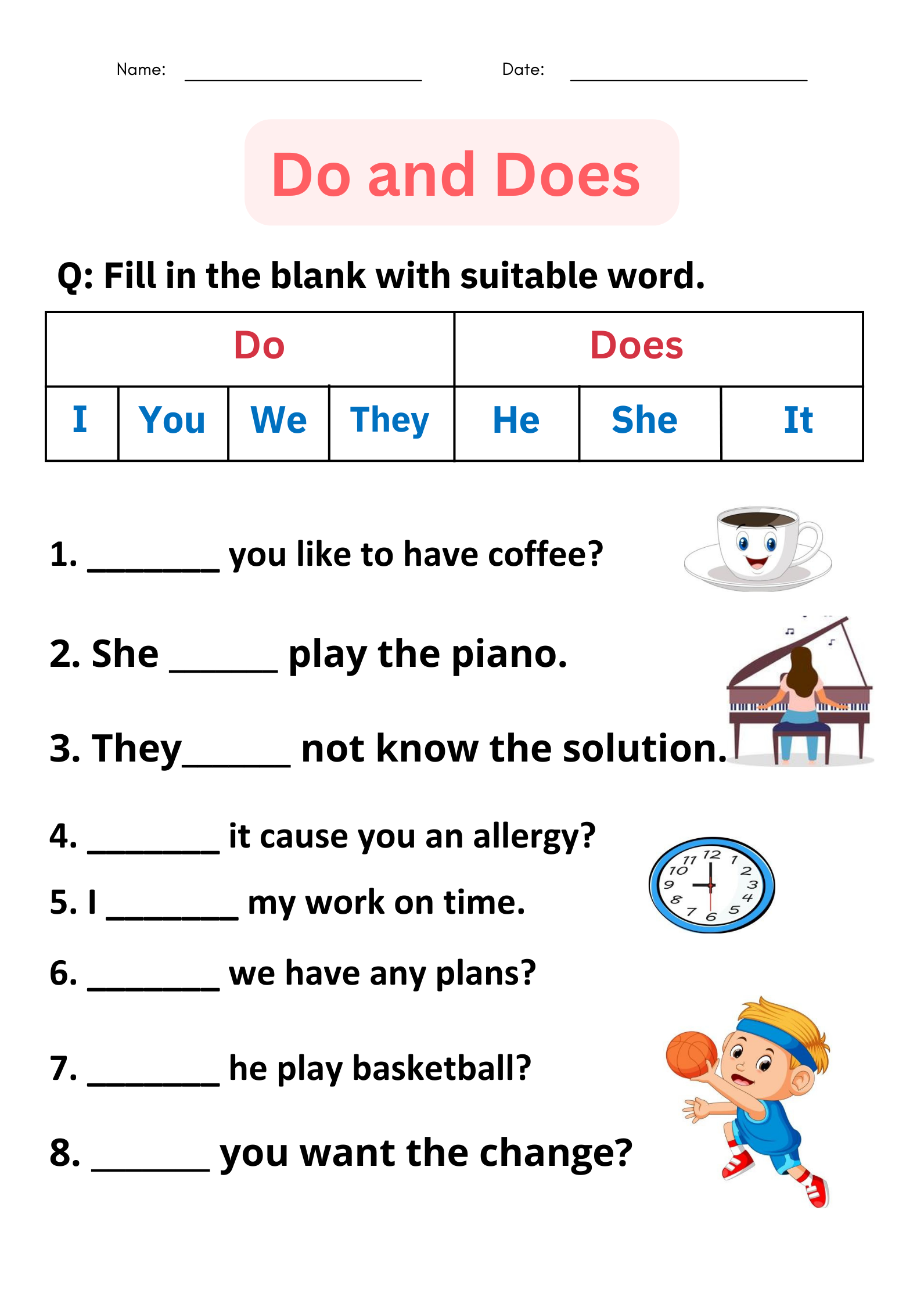
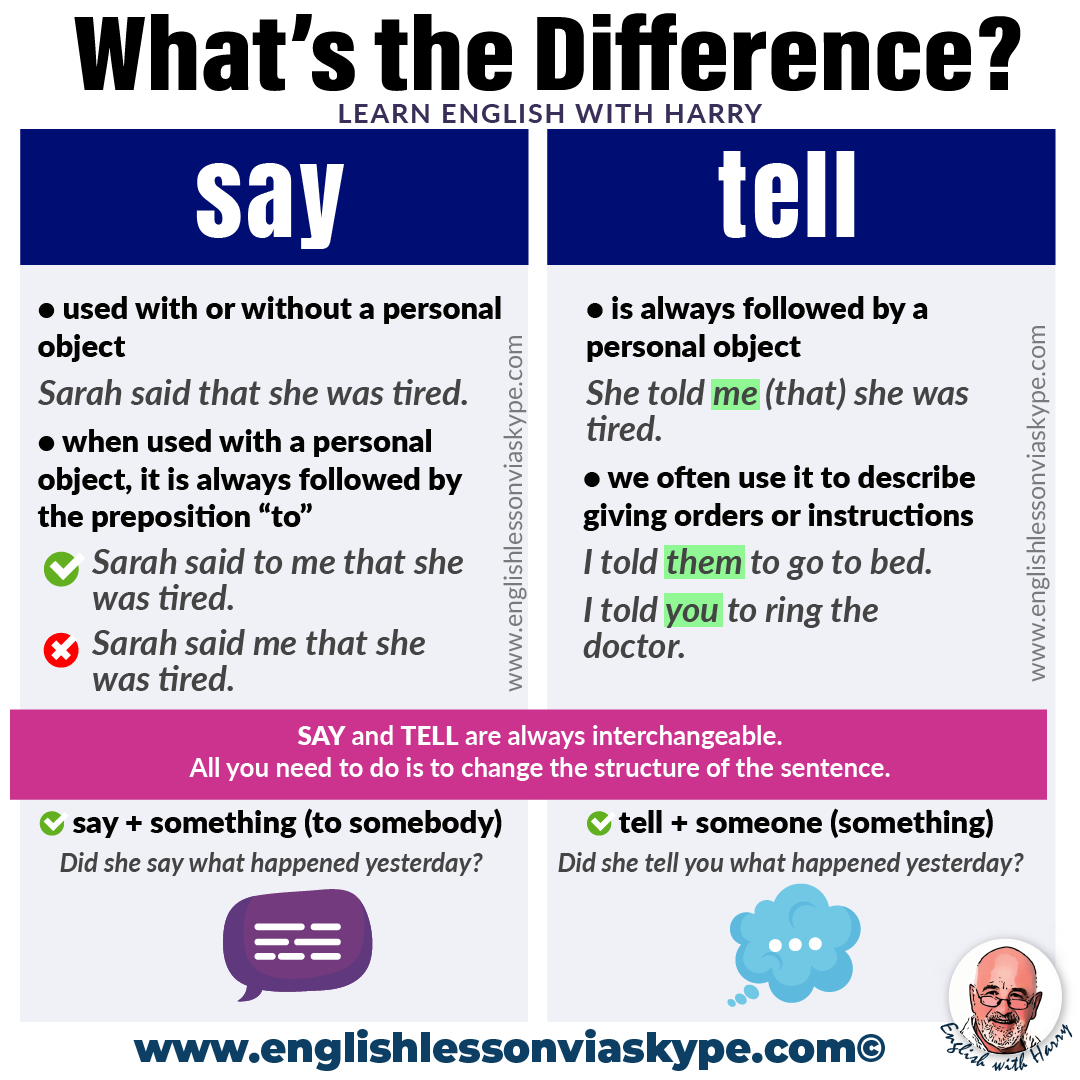
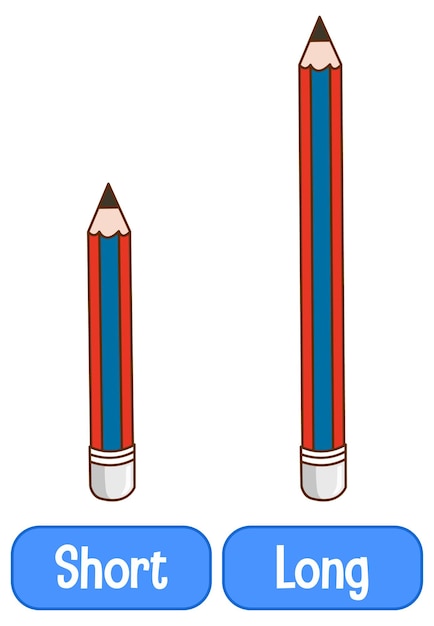
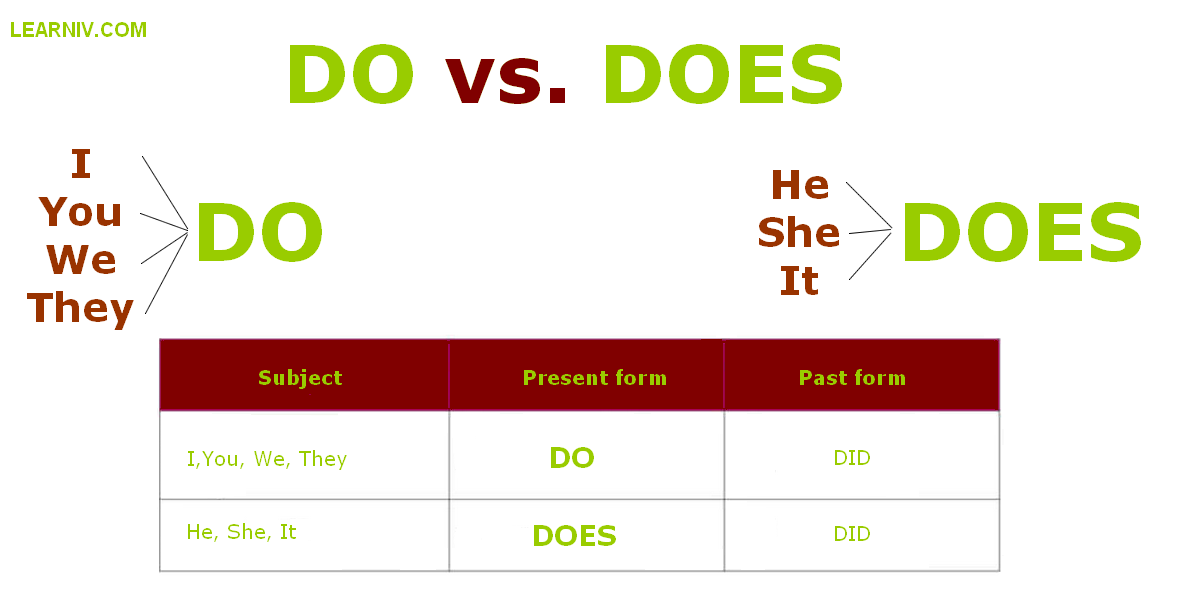